Basics of FPV Drone Motor–Whats a Brushless Motor
The power needed for our FPV drone to fly is aided by motors. In essence, it is the force, energy, or impetus behind those drones that has the biggest impact on each quadcopter’s flight characteristics. Here, even a slight modification to the design arrangement has a noticeable effect on how responsive a quadcopter is.
The majority of fpv drone motors are known as brushless motors because they spin the motor by using three phase power to drive electromagnets. What exactly is electromagnetic now? It is essential to the operation of bldc motor, both brushed and brushless, because it facilitates the transformation of electrical energy into kinetic energy. The motor rotates as a result of the electromagnet’s or permanent magnets’ combined attraction and repulsion. Next we are going to learn FPV motor components.
If you want to learn more about how to choose a brushless motor, read this guide on How to choose fpv drone motor a detailed guide 2024
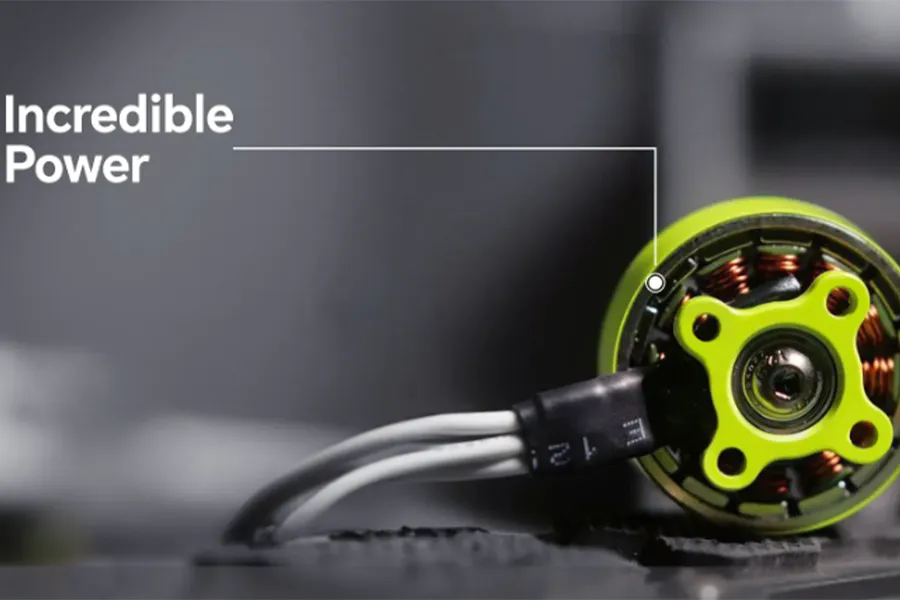

FPV Drone Motor Components
Stator
Brushless FPV drones are just what the name suggests—they lack brushes. The rotor and the stator are its two main motor components.
The motor’s stationary component, known as the stator (windings), is made up of several metal coils. Since the coil wire is twisted into numerous loops, it is protected against short circuiting by an enamel coating. Rotation is produced when an electrical current flows through the stator coils and creates a magnetic field that interacts with the rotor’s permanent magnets.
Stator Laminations
The thickness of the individual metal sheets stacked in the fpv motor stator is called a lamination. More stator plate layers can be stacked for the same motor stator height thanks to thinner lamination.
For improved motor performance, stator laminations should generally be thinner. They assist in lessening the production of heat caused by the Eddy Current phenomenon, which occurs in a fluctuating magnetic environment. FPV motors with thinner laminations are more powerful and efficient because less energy is lost in the creation of eddy currents.

Motor Windings
FPV motor windings are the coiled wires found within the stator of the motor, playing a pivotal role in generating the electromagnetic force necessary for propulsion. These windings typically constitute a three-phase configuration in the context of FPV drones, forming the foundation of a brushless motor system.
The wire gauge, representing the thickness of the wire used in the windings, is a crucial factor influencing motor performance. Additionally, the winding count, denoting the number of turns of wire in each coil, directly affects the motor’s characteristics, such as its torque and speed.
The KV rating of an FPV motor is closely tied to its winding configuration, indicating the motor’s revolutions per minute (RPM) per volt under no load. Generally, motors with fewer turns, or lower winding counts, exhibit higher KV values, resulting in higher RPM and lower torque.
Silver Plated Copper Wires
Copper and silver are known for having outstanding conductivity. However, silver clings very loosely to its outermost electron since it is a bigger atom with more internal electron shells. This implies that it has a higher dissociation rate, which enables the electrons to flow through the metal more freely and transfer heat and electricity. Silver is therefore an even more effective conductor than copper.
Copper wire’s electrical and thermal conductivity can be improved by plating silver onto its exterior, which is advantageous for fpv motors. Budget motors components don’t often use silver-plated copper wires because they are significantly more expensive than regular copper wires.
Multi-Stranded vs. Single Stranded Windings
As the name implies, single-stranded wires are composed of a single copper wire, but multi-stranded wires are composed of three smaller wires that serve as a substitute for the single, bigger wire. When used on high voltage projects, single stranded wires manage heat created considerably better because they are thicker.
Higher operating temperatures can cause multistranded wires to snap or melt more easily. Multistranded wires are generally more efficient because they are packed much closer together and more tightly, creating stronger magnetic fields that in turn produce fpv motors with greater power.
Rotor
The rotor of a motor mainly consists of motro shaft, permanent magnets and motor bell, is the one of the most importent motor components.
Material of Rotor
Aluminum alloy serves as the motor bell’s primary material. The motor’s durability is determined by the metal selected for the motor base and bell. FPV motors typically employ two types of aluminum alloy: 7075 and 6082. The number indicates the various grades and series of aluminum alloys as well as their chemical makeup.
In summary, 6082 is more formable and ductile, whereas 7075 is more rigid and resilient to collisions. Prior to 2016–2017, 6082 was used, but 7075 is now more frequently found in fpv motors since it is believed to be more resilient to impact.
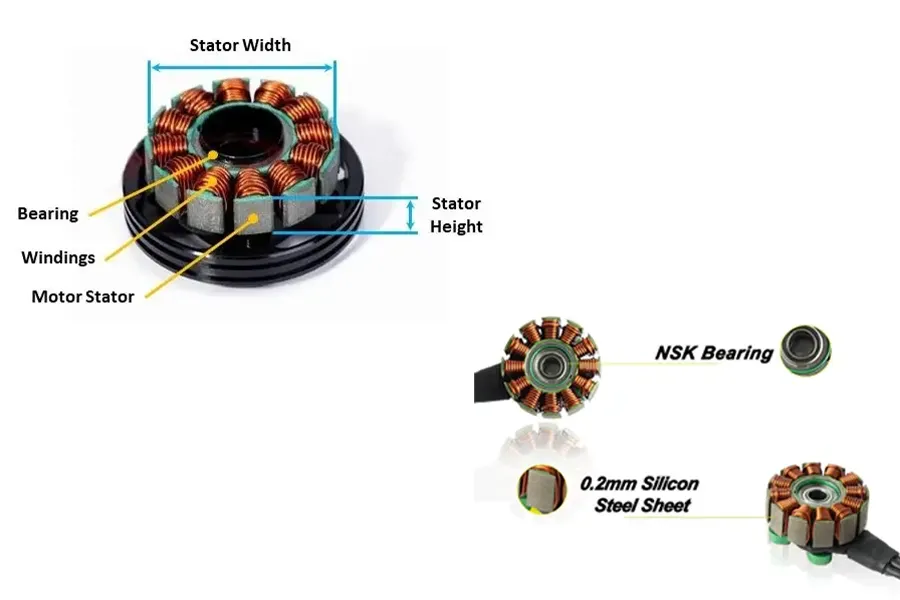
Design of Rotor
Two-piece bell designs and Unibell designs are the two different kinds of bell designs. The two-piece bell design, a conventional and often used motor architecture, consists of an aluminum portion that has been machined on top and a steel flux ring that is bonded underneath. A thin protective sheath, resembling a bell made of aluminum, extends down over a steel flux ring in the Unibell design.
The Unibell design’s one-piece construction increases the fpv motor’s weight slightly compared to two-piece bell designs, but it also makes the design more durable and less likely to slip, which is a typical problem with some two-piece bell designs. In a severe collision, a two-piece motor may experience the flux ring separating from the bell’s upper section, which would cause the fpv motors to fail. But with the Unibell design, this is practically unheard of because of the large adhesive area that guarantees a solid and reliable binding between the two parts. The extra durability offered by the Unibell design, in my opinion, justifies the expense, even with the little weight penalty. In the end. It’s worth it to make the small weight gain in exchange for the significant resilience gain.
If you want to learn more about how to motor size, read this guide on What Size Motor Do I Need for My Drone?
Poles and Magnets
A 22xx or 23xx FPV motor typically consists of 14 magnets and 12 poles. This number will be identified by a symbol similar to 12P14N. FPV motor performance is directly impacted by the number of poles. Greater power production can be achieved by increasing the iron content of the stator when there are fewer poles. Nonetheless, a magnetic field that is more equally dispersed results from having more poles. This consequently results in a motor that runs more smoothly and gives the bell’s rotation more precise control. It is an indispensable motor components.
Magnet Type
The magnets in a motor have a significant impact on the motor’s power output. In comparison to an expensive motor with stronger magnets, a cheap motor will generate less thrust due to its weaker magnets. Even curved magnets that follow the curve of the rotor are a feature of certain more expensive motors. Brushless motor magnets are rated N52, N54, and so on according to their magnetic strength; the higher the number, the stronger the magnetic field the magnets produce.
Bearings
Bearings is another important motor components. It is not the diameters themselves that determine a bearing’s size, but rather the differential between its outer and inner diameters. Larger balls (or marbles) can fit into wider bearings. At high speeds and RPMs, smaller balls give more stability and smoothness, while larger balls offer more durability and crash resistance. Certain motors are advertised as having “ceramic bearings,” which substitute ceramic balls for steel ones in operation. Although these bearings are smoother, there is a greater chance of failure.
The maximum shaft size that can be employed is also determined by the inner diameter of the bearing. A 9mm x 4mm bearing provides a nice mix of smoothness and endurance. NSK, NMB, and EZO are among the popular Japanese brands of bearings used in FPV drone motors. Even though EZO bearings are frequently hailed as the greatest, it might be difficult to measure how much better they are than competing models. It’s also critical to take into account the potential for producers to use fake goods in place of real ones.
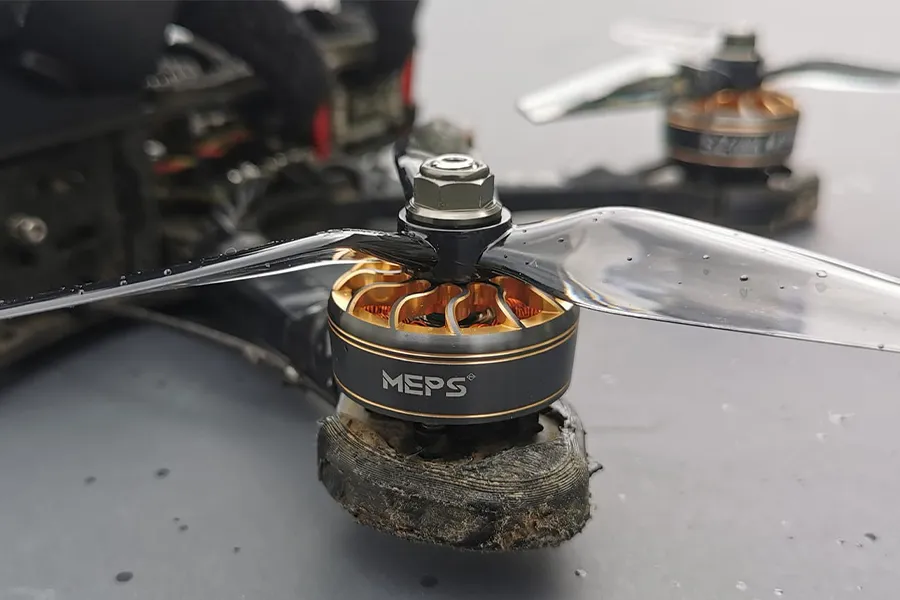
Motor Shaft
Since the fpv motor shaft is in charge of firmly mounting the propeller, it is an essential fpv drone motor component. In an effort to lighten the engine, modern models employ hollow shafts rather than solid ones. This offers advantages as well as disadvantages. Although hollow shafts plainly lighten the motor, they are not as resilient in collisions. Shaft replacements require replacing the motor’s whole rotor. Hollow shafts are a bad thing for builders on a tight budget, but they are the best option for those trying to conserve every gram.
FPV Motors Mounting
A fpv motor’s mounting patterns are important as well because they should work with whatever frame you decide to utilize it in. These days, most5″ quads use motor sizes between from 2205 to 2407. All of the fpv motors feature mounting patterns of either 16 x 16 mm or 16 x 19 mm. This shouldn’t be too much of an issue because all contemporary frames accommodate all those mounting methods.
M3 screws are used in the mounting holes of these fpv motors. Use screws with a thread length that is 2 mm greater than the arm thickness; for instance, use 7 mm screws for 5 mm arms and 8 mm screws for 6 mm arms.
Learning how to rotate the FPV motor direction can help you install the motor more effectively :