Introduction:
This video offers a concise guide on assembling a 3.5-inch CineWhoop drone with a focus on installing a digital video system, highlighting key assembly steps and flight capabilities.
- Guide Overview: How to assemble a 3.5-inch CineWhoop drone with a digital video system.
- Key Components: Speedyb35 frame, MEPS 2004 motors, digital FPV.
- Tools: Hex wrenches, soldering iron.
- Assembly Steps: Frame setup, electronics installation.
- Betaflight Setup: Configuration for optimal performance.
- Motor Testing: Ensuring correct motor order and spin direction.
- Flight Insights: Agility and power evaluation, propeller upgrade suggestion.
- Final Note: Drone ready for flight, balance of power and efficiency highlighted.
Video Overview
In today’s video, we’re diving into the exciting process of assembling a 3.5-inch CineWhoop drone equipped with potent motors and a digital video system. While we focus on a digital setup, converting to an analog system is straightforward for those who prefer it.
Initial Impressions and Flight Test
Unveiling the Drone
We begin by unboxing and preparing the drone for its maiden flight. Equipped with a new battery, the drone is remarkably agile, thanks to its 2507 motors. Despite using a powerful setup, I notice the propellers could use an upgrade for even better performance. Throughout the flight, the drone showcases its agility and power, although the batteries deplete quickly due to their high performance.
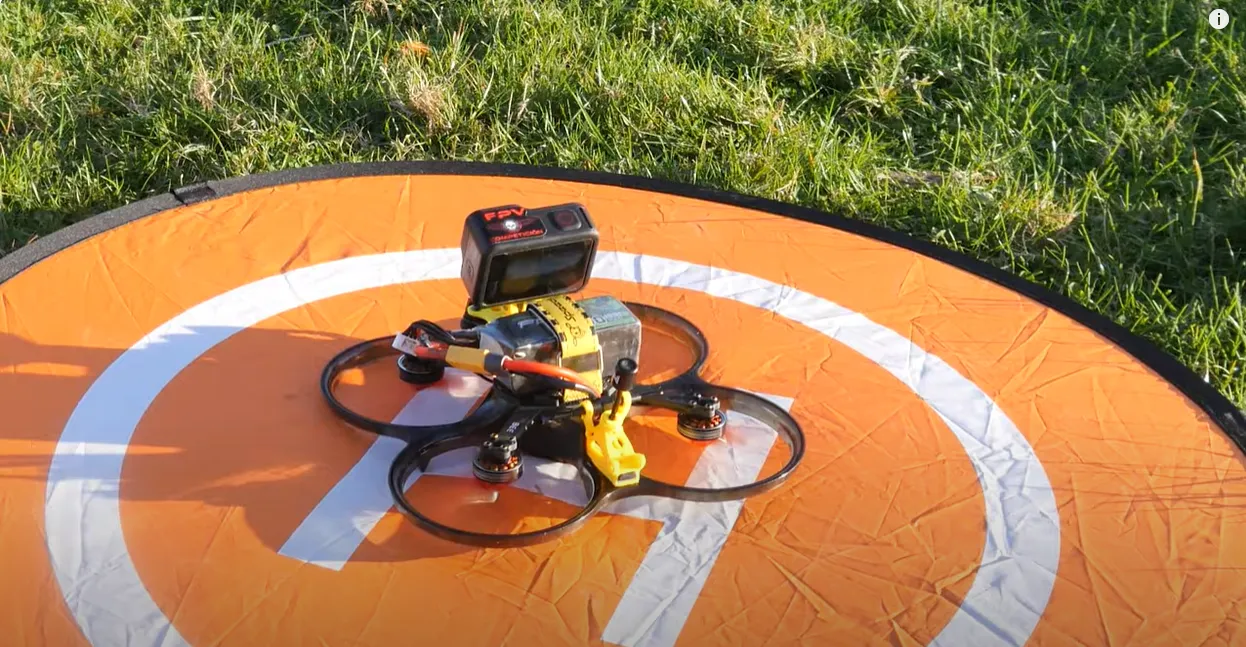
Flight Performance
Flying without a GoPro, the drone’s agility shines, even in windy conditions. The experience suggests that with a few adjustments, including possibly changing the propellers for ones with more pitch, the drone could handle additional weight, like a GoPro, without sacrificing too much agility or power.
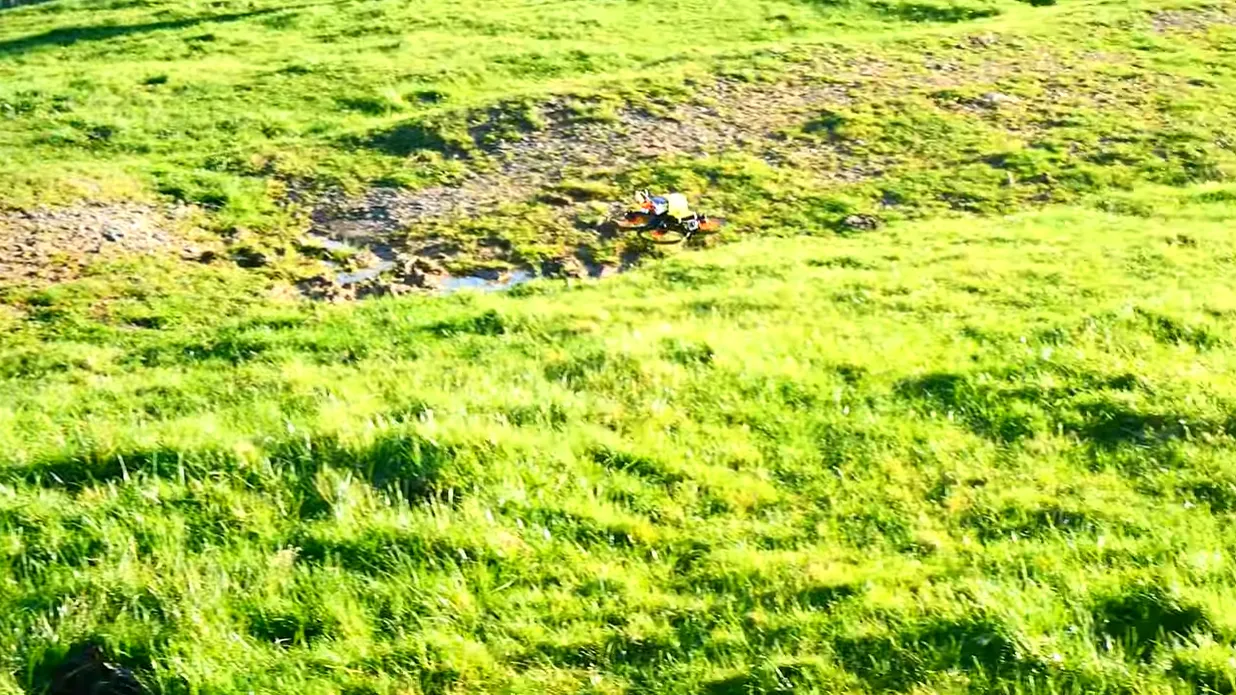
Step-by-Step Build Guide
Gathering Components
For our build, we require a frame, in this case, the Speedyb35, alongside matching electronics from the same brand for the controller and ESC, known as a stack. Additionally, we’ll need an FPV video system compatible with DJI, MEPS 2004 motor, an LRS receiver, and propellers.
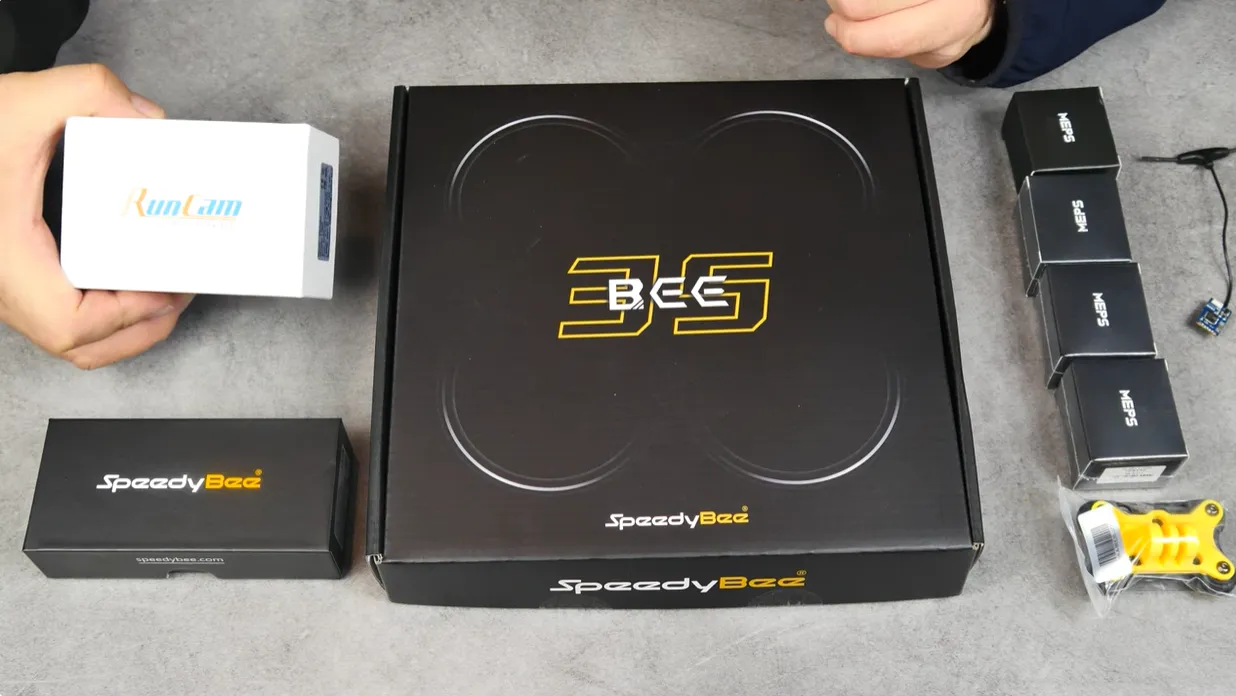
Required Tools
- Hex wrenches (2.0mm and 1.5mm)
- A soldering iron (I’m using the TS100)
Frame Assembly
The assembly process starts with the frame. We’re working with the Speedyb35, a budget-friendly option that doesn’t skimp on quality. After unboxing, we find comprehensive assembly instructions, various TPU parts for damping and customization, and all necessary screws and mounts.
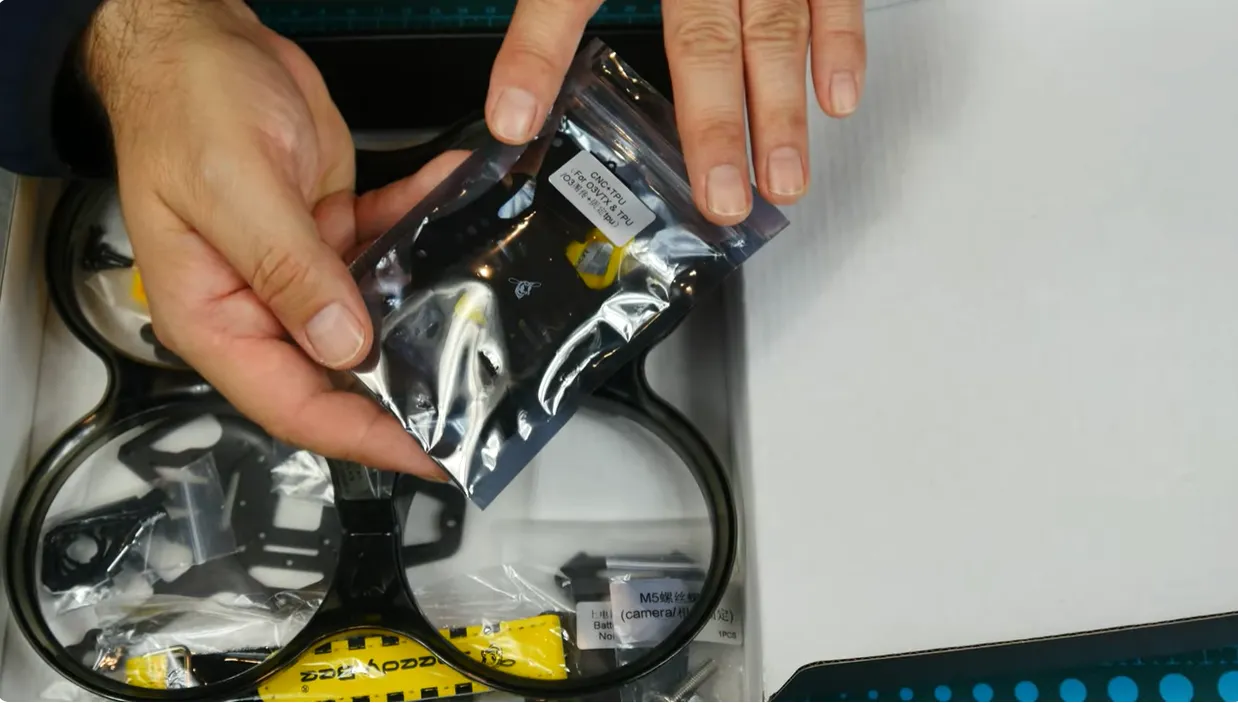
Electronics Installation
- Preparing the ESC
We begin by soldering the XT60 battery connector to the ESC, ensuring a strong connection for power delivery. This step requires careful soldering, especially with thicker wires, to ensure a secure and reliable connection.
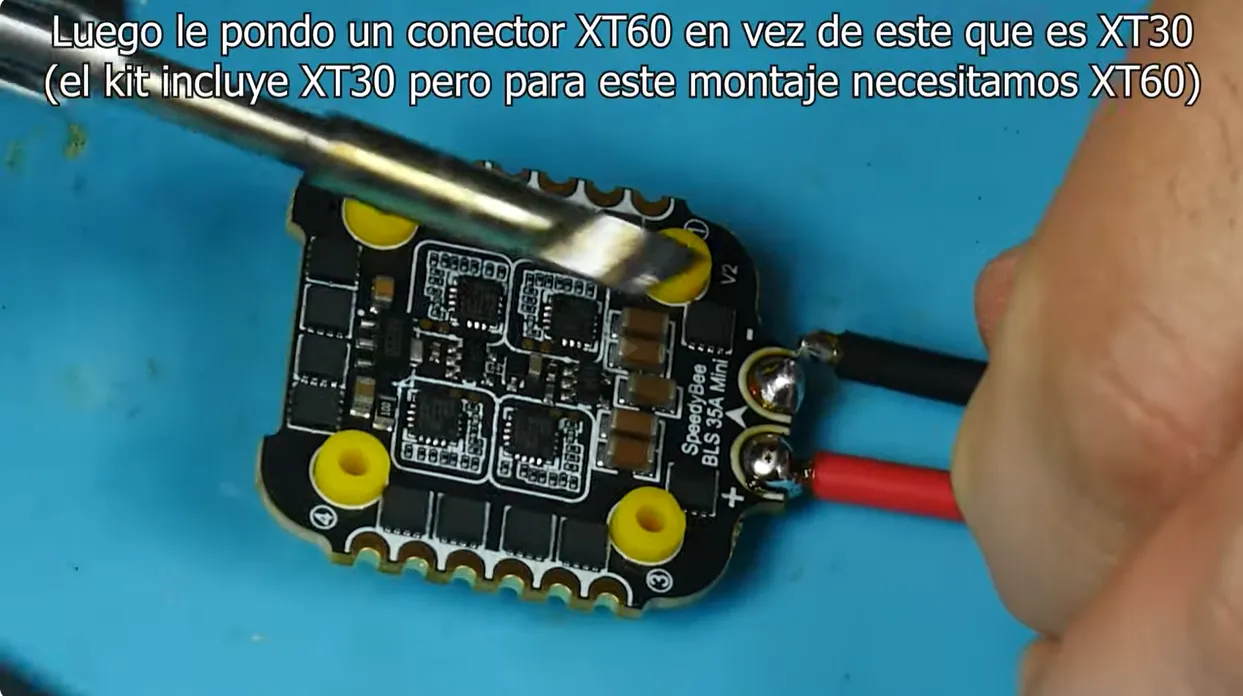
- Motor Attachment
Next, we attach the MEPS 2004 motor, using the provided screws to secure them to the frame. It’s crucial to arrange the wires neatly and trim them to length before soldering them to the ESC, following the correct order for optimal performance.
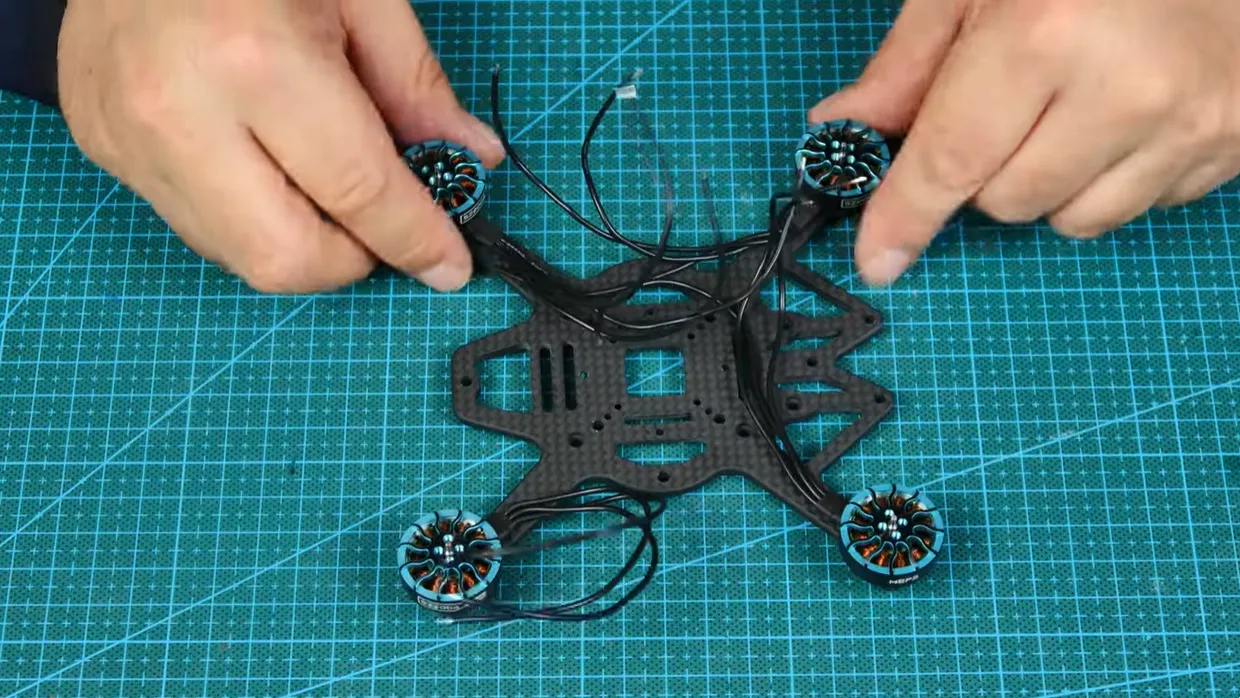
- Flight Controller Setup
The flight controller is mounted atop the ESC. We make sure to connect them properly, paying close attention to the alignment of pins and sockets. This step is crucial for the communication between the ESC and the flight controller.
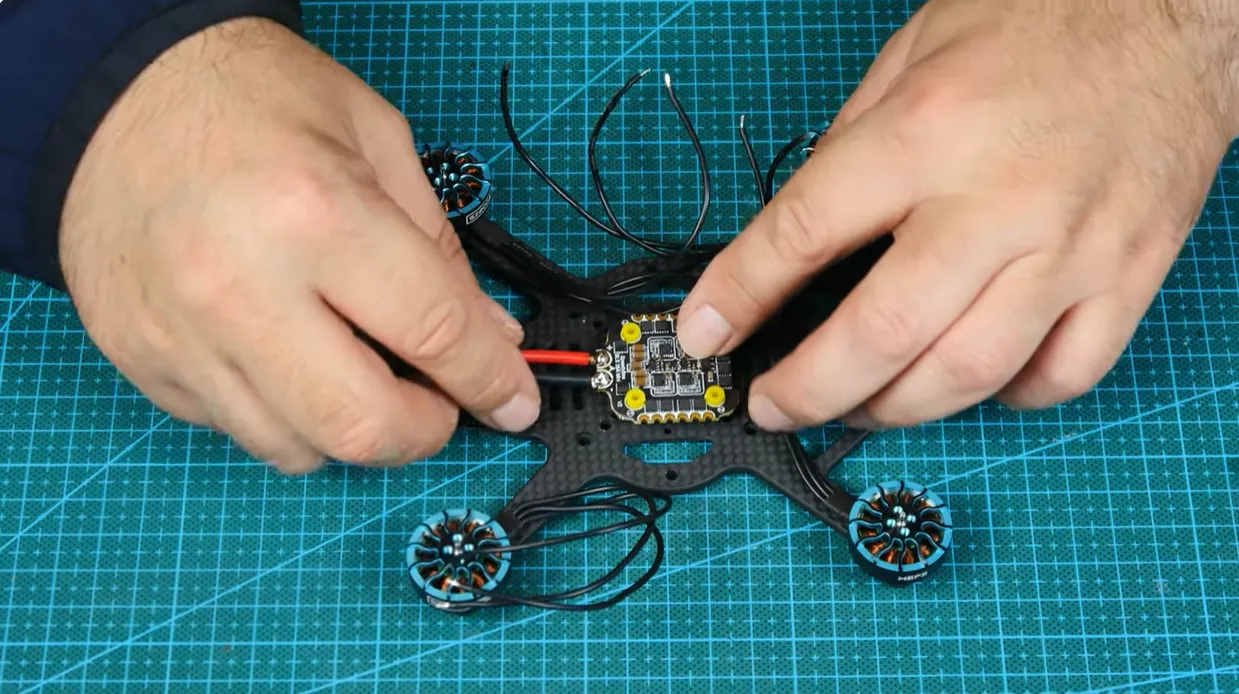
- Final Touches
With the motors and flight controller in place, we focus on connecting the radio receiver and the FPV system. For this build, we opt out of adding GPS, considering the CineWhoop’s intended use for close-range flying.
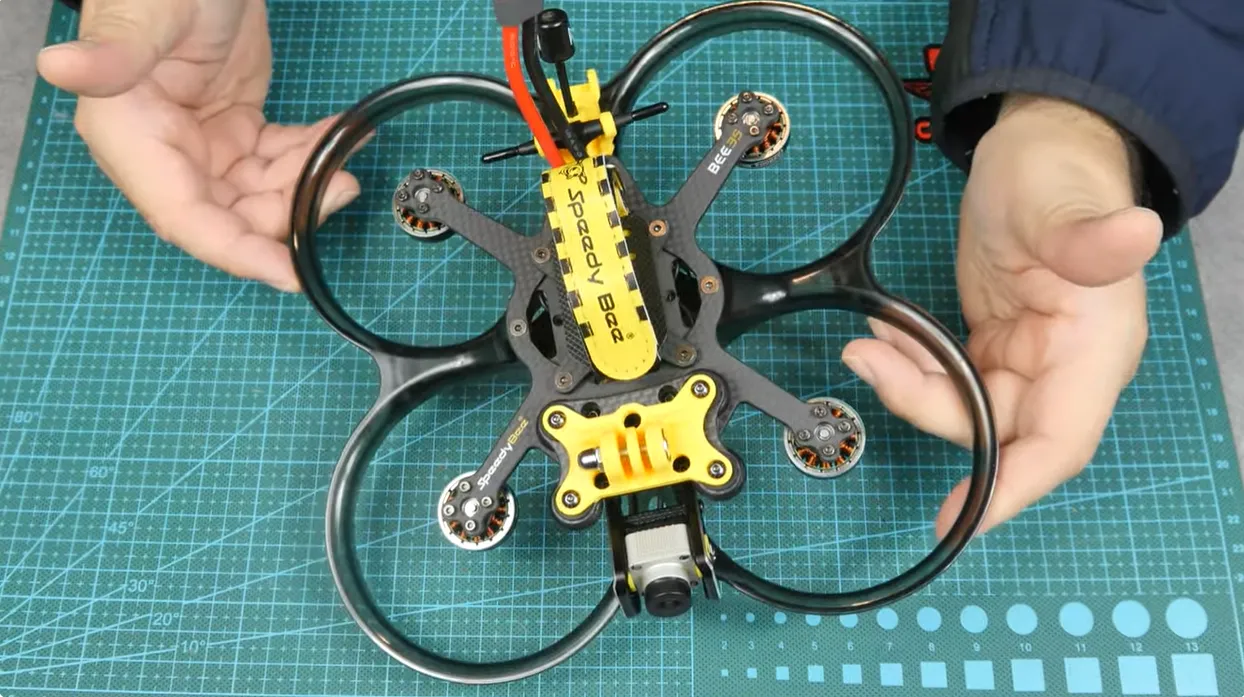
Connecting and Configuring in Betaflight
Preparing for Configuration
Once we have the drone connected to the USB, it’s essential to make the necessary adjustments in Betaflight. For clarity in setup, we will place the drone on the ground and prepare to connect the cables. In my case, I’ve already borrowed the necessary cables, but I will explain the process as if I were lending them to you.
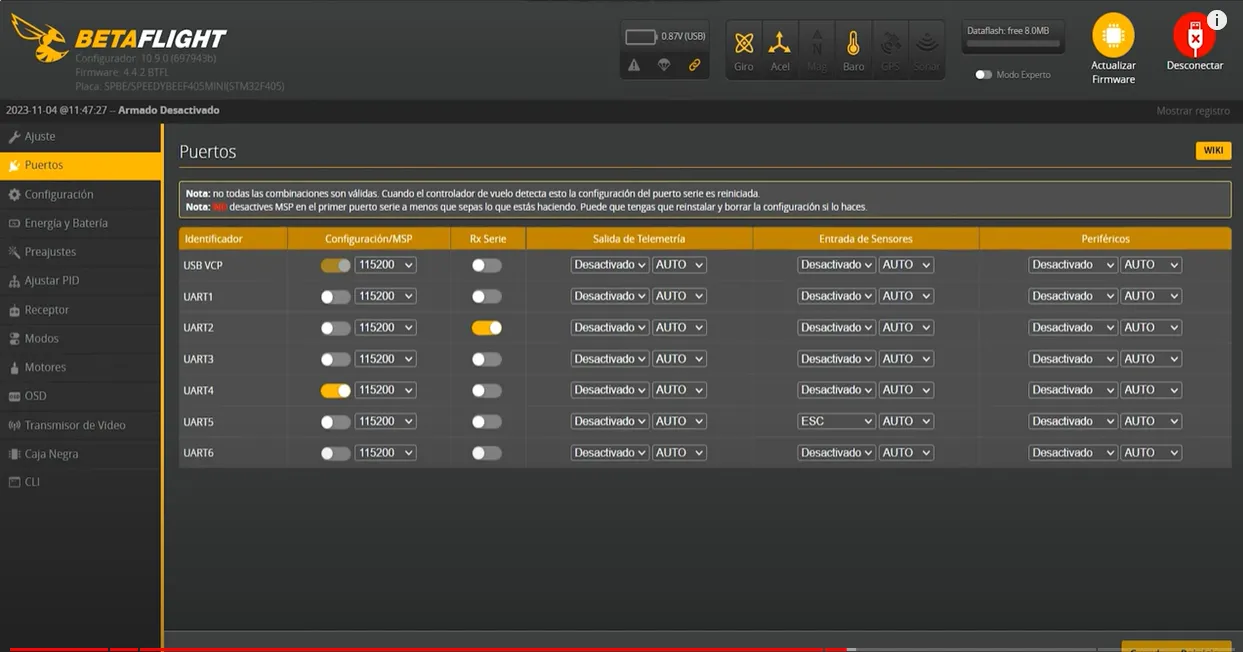
Wiring Details
The white cable corresponds to the ‘T’ (transmit) pin and will, therefore, be connected to the ‘R’ (receive) pin on the drone, and the yellow cable, corresponding to ‘R’, will be connected to ‘T’. The ‘T’ pin, in my setup, is located towards the corner. Next in the sequence is the ‘R2’ pin, to which the white cable (T) connects, followed by the positive and ground cables.
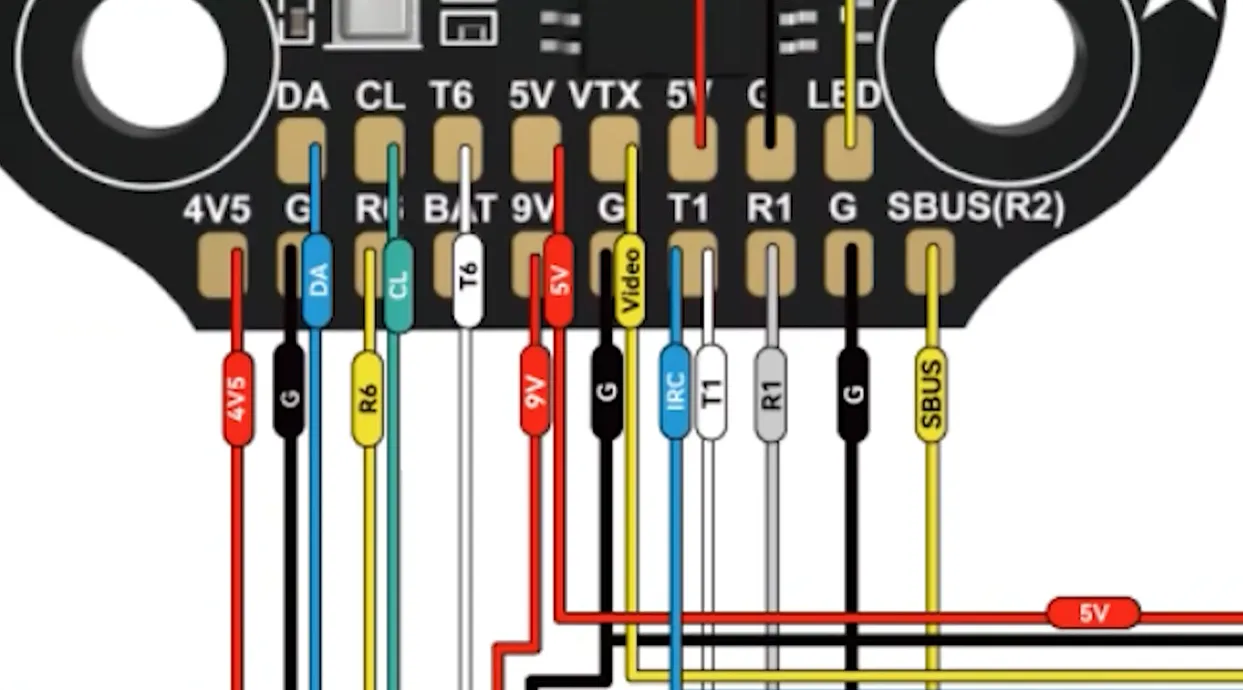
Installing the Video System
After the wiring, the next step is to install the video system. Assuming there are no further adjustments, we proceed to save the settings for the motors and move on to the OSD (On-Screen Display) configuration.
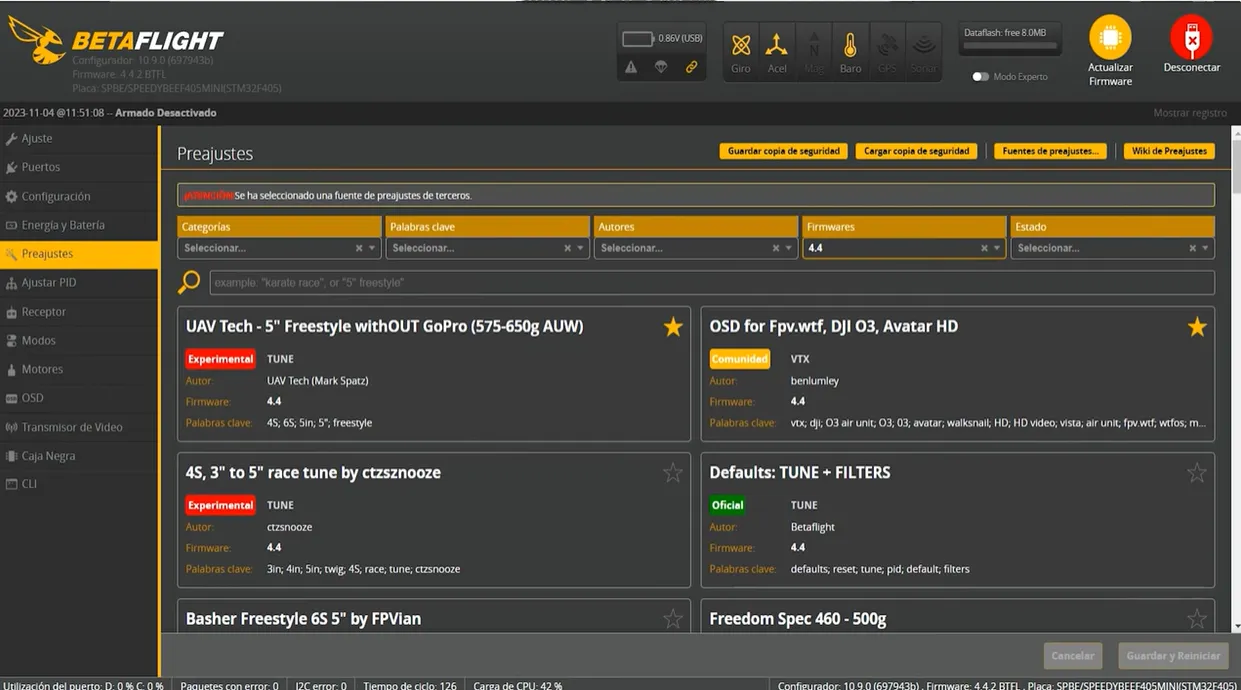
OSD Configuration
In the OSD section, adjustments are made based on whether you’re working with HD mode for O3 systems or normal mode for V2. Since I’m working with V2 in non-HD mode, I’ll only configure essential elements like voltage, milliamperes consumed, drone identifier, RSSI (Received Signal Strength Indicator), and the 2s timer, which indicates how long the drone has been armed. These settings are straightforward and require no further modifications.
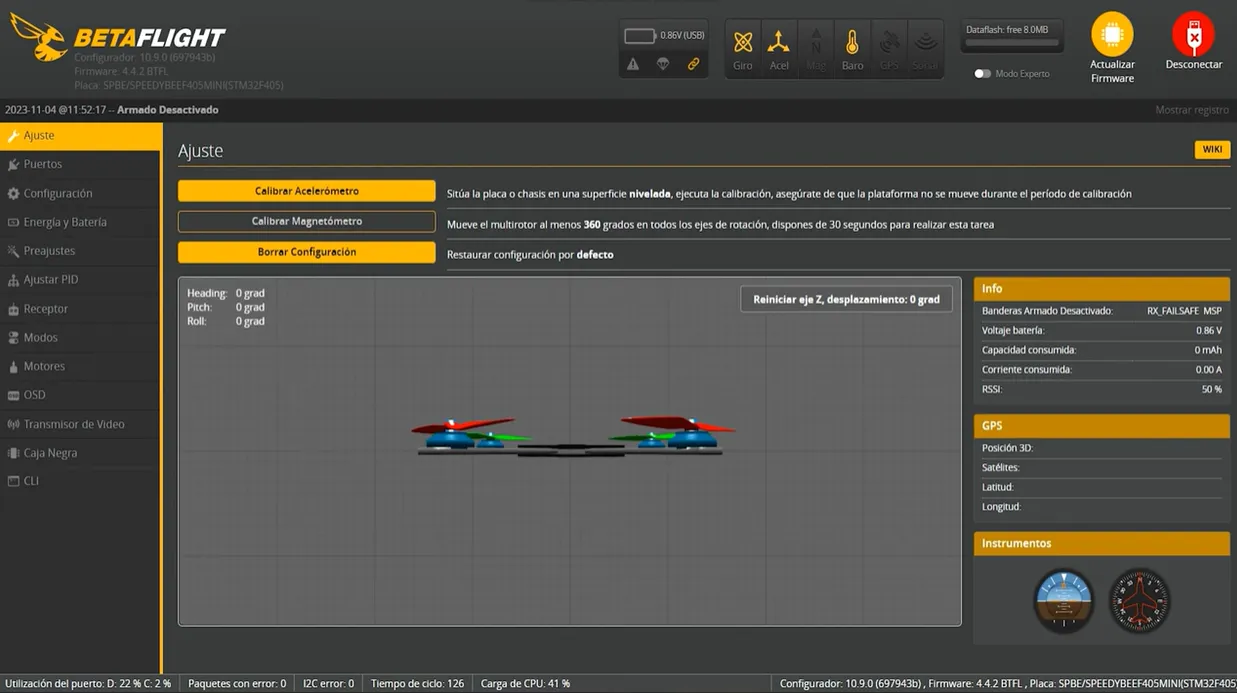
Testing and Adjusting Motors
Motor Test
The next crucial step is testing the motors. This process involves checking the order of the motors and ensuring they spin correctly. If not, we must reorder them accordingly. After verifying the motor order and direction, we save the settings.
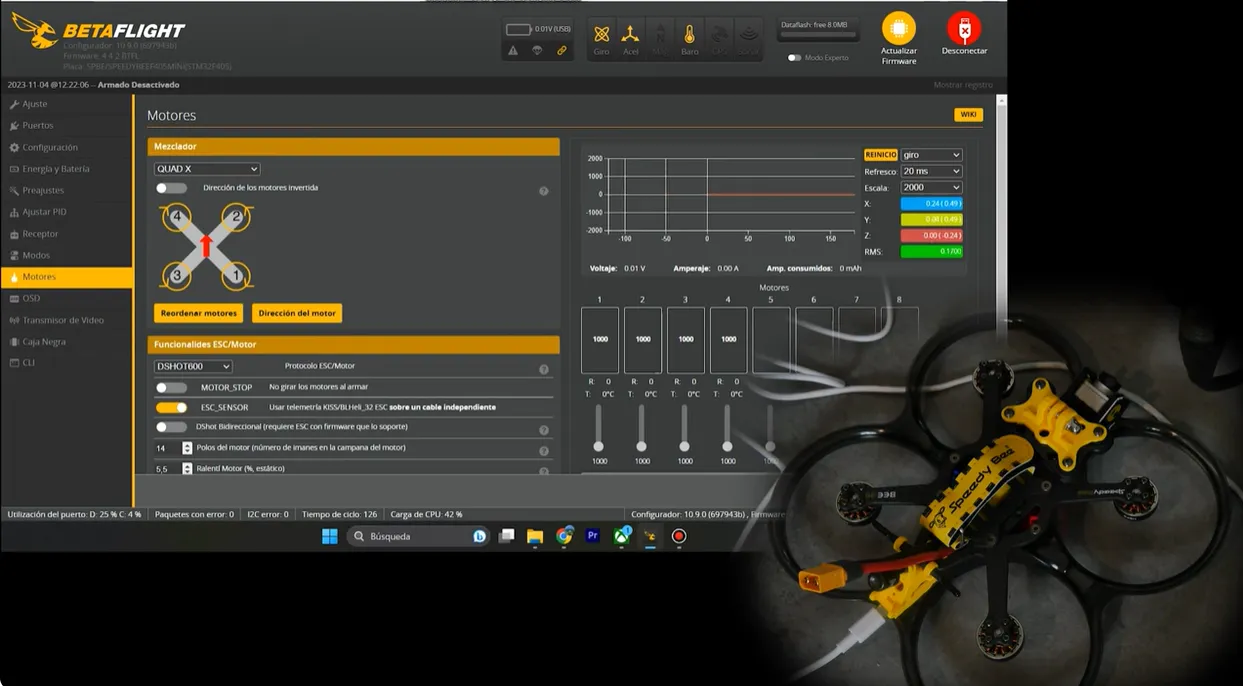
Final Adjustments
With the motors configured correctly, the final step involves adjusting their direction to ensure that the propellers spin outward, enhancing the drone’s performance. After saving these adjustments and a final check, the drone’s engines are ready.
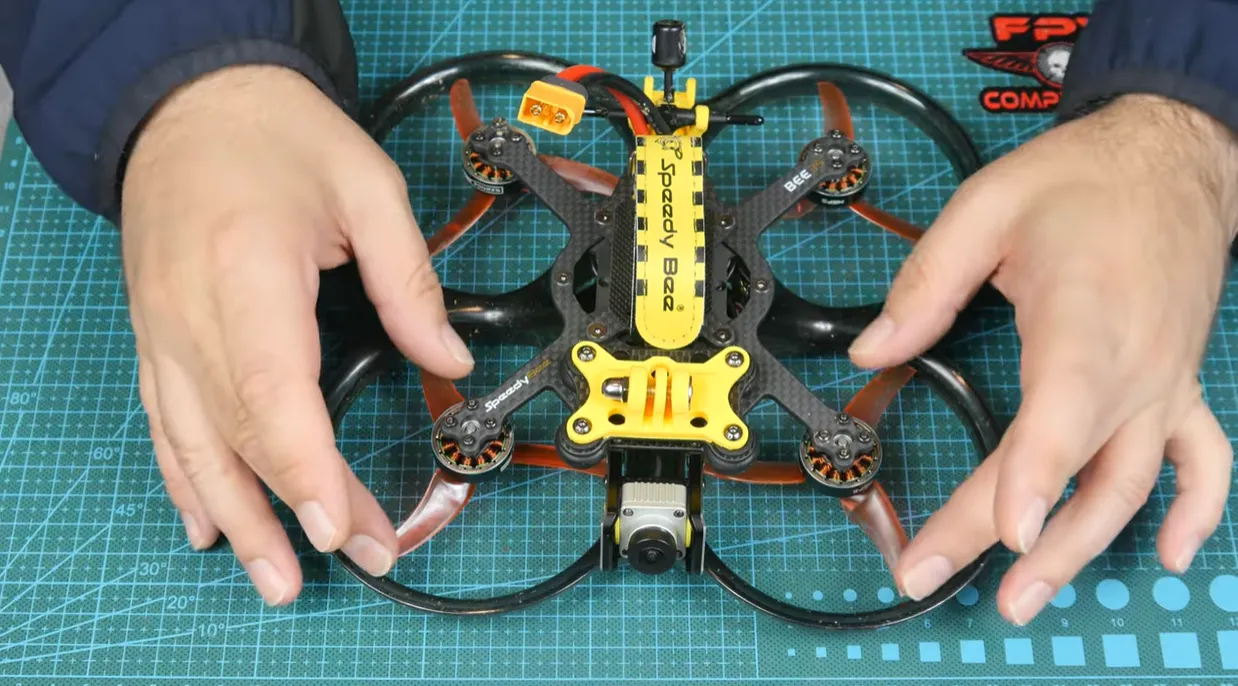
Conclusion: The Drone is Ready to Fly
The completion of these steps signifies that the drone is ready for flight. Earlier in the video, I showcased its flight capabilities, highlighting its performance. For those seeking more power, upgrading to larger motors is an option. However, the current setup offers a good balance of power and flight time. An important note is the potential propeller upgrade, which I recommend for optimal performance.